【連 載】CSTが提案するプラントライフサイクルデータマネジメント
第2回 PLDMにおけるレーザースキャン技術の展開 ~3Dモデルの活用~
千代田システムテクノロジーズ株式会社 岡林 健 2015.9.25 |
|
第2回の本稿では、CSTが提案するPLDMにおける3Dモデルの活用方法を紹介する。昨今のレーザースキャン技術の進化により、海外では建設現場や既設プラントから3次元情報を取得し、活用することは一般的となっている。少子高齢化が進む日本では、プラントの安全操業と、技術伝承への対応がせまられているが、3次元情報から得られる3Dモデルの活用を通して、いかにPLDMではこの課題に取り組むかを説明する。
以前は手描きされた設計図面の青焼きや紙図面が、設計図書として当たり前のように使われ、現場や事務所で目にする事ができた。そんな中で1960年代に登場したCADは、当初、一企業で使用するにはあまりにもシステム自体が巨大であり高価なものであった。しかしながら、その高い価値や将来性から、多くの企業が多額の資金を費やし改良開発が続けられた。
その結果、1980年代には各分野に特化したCADが開発され多くの企業においても使われるようになった。1990年代後半には3D CADが登場し、3次元での設計が始まる。3D
CADといっても、登場時は専用の高価なハードを必要とし、独特のインタフェースを用いるため、CADに関する専門スキルが求められた。その後、ハードウェア技術の進化と低価格化も相まって、急速にCADが普及することになる。納品図書として電子化が指定された時代背景から、積極的なCAD図面のTIFF化やPDF化がすすめられ、CDなどへメディア化された。
しかしその反面、必要な時に必要な場面で利用できる状態にはない電子図面は、利用されにくく、実際のプラント施設の状態と乖離していく。たとえコストをかけてCADデータを最新に更新維持出来ていたとしても、実際に使用する時は紙に印刷して使用される事が主流である。CADデータは、あくまで図面としての利用であり、その多くは当然のように未だ2Dの紙図面である。
一方、3D CADは、紙での共有は難しい。そもそも紙の図面と異なり3D CADで描かれた3Dモデルは現場へ持ち出すことが不可能であった。加えて、3D
CADは高価であり操作方法が難しい上に、3Dデータの受け渡しになると、企業間は言うに及ばず、同一企業の部門間でも、CADソフトの違いやバージョンの違いなどの壁があり、その利用には困難を極めた。
3D CADの操作には高度なスキルが必要であり、エンジニアが直感的に操作するには複雑すぎるインタフェースも、いまだ使用上の壁となっている。国内の優秀な熟練技術者にとっては、2D
CADで実現できることをコストのかかる3D CADで行う必要もない。2D CADと比較して3D CADのメリットや使用目的が不明確であればなおさらである。
昨今、国内のプラント設計でも3D設計がなされるケースが増えてきた。2D設計と比べて3D設計により得られるメリットは大きい。現実に存在する鋼材や部品を使ってプラントを建てるのであるから、それらの部品を電子カタログデータとして保持し、3D
CADで空間配置していく。いわゆる3Dモデリングによる3次元設計である。
2D CADを用いて3次元を想像しながら設計するのではなく、そのまま直感的な3D CADを用いて設計業務が進められる。施工用図面や官庁申請図面を含め、必要な各種2D図
面も3D CADから自動生成される。課題であったCADを含むデータの互換に関しては、ISO15926にみられるように標準化も進んでおり、多くのCADで互いにデータのやりとりができるように改良されてきている。
近年のクラウド技術やタブレットの進化は、難しかった3D CADモデルの現場への持ち出しを可能とした。紙での受け渡しと異なり、PLDMで統合化されたCADデータであれば、部門を越えて必要時に参照し活用可能となる。
3Dモデルの大きなメリットは、なにより視覚的に分かりやすいことである。2D図面は空間構造を想像する必要があり、図面を読む高い能力を必要とする。さらに想像された空間構造は、その人の経験によって想像される形状やサイズが異なり、図面を介してのコミュニケーション上でのエラーとなる。それに対し、実態そのものである3Dモデルは誰が見ても一目瞭然で理解しやすい。
図1. CADデータの電子統合化 |
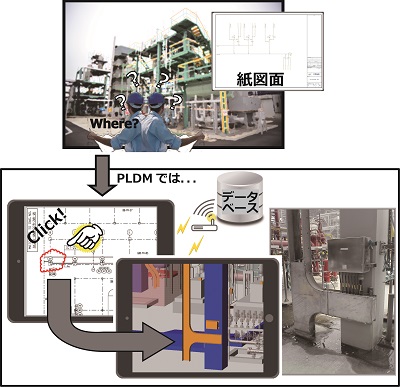 |
3Dモデルは画面内で対象物を回転させ、あらゆる方向から状態を確認できる。コミュニケーションにおいて正確に意図を伝えられることは必須である。現場での作業検討の際に、あらかじめ状況が想定できているか否かの重要性は言うまでもない。
図2. 対象部品の検索・視覚化 |
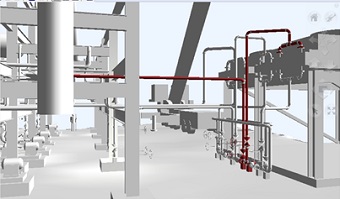 |
3Dモデルがあれば、装置交換や操作時に安全な作業スペースが確保できるか、新設装置が隣接する部品とぶつからないか、機材の搬入経路上に障害物がないかといった干渉チェックが計画段階で事前に可能となる。さらに3Dモデルからは長さや、体積・表面積・質量・重心等の
情報が得られるため、解析用データ
としての利用もできる。
また属性データの付加された3Dモデルからは、使用部品の集計や使用鋼材の強度解析などのデータを得ることもできる。あるがままの3Dモデルからは当然ながらISO図や配管図の自動抽出ができる。さらに、必要配管のみを表示しての部品構成や接続情報の確認も可能となる。これは、プロットプランとの整合性確認やP&IDを最新化する際に有効活用できる。3Dモデルが最新に維持されていれば、必要な情報を何度も現場で確認したり、寸法を測定しなおしたりするのに比べて安全で低コストである。
さらに設備保全管理システム(CMMS)やプラント情報管理システム(PIMS)の情報と連携することで、設備の運転状況や、耐用年数、交換時期による色分けや、特定部品の検索など、視覚的に表示することが可能となる。3Dモデルを用いれば、直感的で分かりやすい指示書を作成することができるだけでなく、使用する部品や指定工具での作業性など、周辺空間の状況確認も可能になる。作業現場では、作業手順をタブレット上の3D
PDFなどで確認することも考えられる。
ここまで述べてきた3Dモデルであるが、それを手にするためには、3Dデータが必要である。そもそも2Dで設計されたプラントでは3Dモデルが存在しないこともある。3Dデータが存在していても実際の状態と合っていない場合もあろう。そこで有効なのが3Dレーザースキャンである。
図3. アクセス性の確認 |
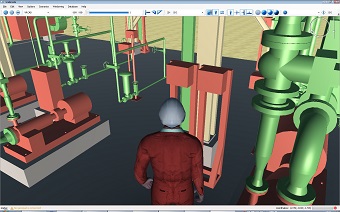 |
近年格段に進歩したレーザースキャン技術により、実物プラントから3Dデータを取得し、利用することが実際に可能となった。精度よく短時間で対象物の3次元座標情報を、まるでカラー写真のように取得できる。その情報があれば、現実のプラントを正確にコンピュータ上に再現できる。まさにバーチャルプラント
の実現である。
レーザースキャンで得られた3Dデータには、図面には描かれないものも表現される。各種機器は実寸で表示され、電線や張り出し、足場や資材置き場、建機や車両など、スキャンされたもの全てが3Dデータ化される。
つまり現実のプラント設備があるがままに、3次元データ化されPLDMの3Dデータとして取り込まれるのである。その結果、PCやタブレットを用いて、正確な作業指示の伝達やリアルな運転操作教育や操作シミュレーション、技術伝承のためのトレーニングなどが可能となる。
図4. 視覚的な作業指示伝達 |
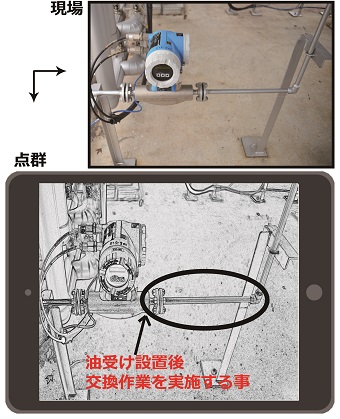 |
さらに耐震、耐久性評価や高経年化による傾きやたわみなどの変移解析もレーザースキャンで取得される3Dデータで可能となる。その結果、耐震補強の必要性や交換時期の算出ができ、予防保全や補修計画に経済的に役立てられる。
また、レーザースキャンでの計測は、計測対象から離れた場所から行えるため、対象物に触れる必要がない。そのため、レーザ光が届く範囲の高所や高温部、低温部、さらには光の届かない暗い部分も安全に計測可能である。
SDMの着工前後や改造工事の前後、さらには運転条件変更の前後にレーザースキャンを行うことで、装置状態を比較し解析することが可能となる。
高度成長期を支えてきたプラントと、その資産である安全操業のための設計や、運転上で受け継がれてきた優秀なベテラン社員の経験やノウハウは、埋もれさせてはならない。ますます少子高齢化が進む我が国において、技術伝承はまさに今必要なのである。その対応にPLDMは有効に活用され得るソリューションである。
PLDMで提案する3Dモデルの活用を含む新しいICT技術の導入は、日々の安全操業の手順を置き換えるものではない。電子化され統合されたデータは、シームレスにどこでも利用することを可能とし、関連部署のコミュニケーション連携をより確実にする手助けとなる。さらに、現場における勘や経験は安全操業において重要である。その勘や経験に頼らざるを得なかった部分を補完し、天候、時間、場所によらずいつでも何度でも使えるバーチャルプラントによって、可能な限りICT技術を利用して視覚化することで、よりわかりやすく効率的な技術伝承を支援できる。
このようにPLDMソリューションの利用を通じて日々の情報を蓄積し視覚化することで活用価値を高めることが可能となる。安全で最適な運転と設備の維持強化を達成するため、PLDMで高度に価値化されたデータの有効活用を提案する。
次回は、3Dモデルのみでは実現できない、プラントの状態を可視化し、プラントの運転支援や、安全管理を実現するPLDMのフロントエンドソリューションを紹介する。
|
|
|
|